รายละเอียดระบบ
ลูกค้าเป็นโรงงานอุตสาหกรรม ซึ่งใช้นํ้าที่ผลิตจากระบบรีเวิร์สออสโมซิส เพื่อใช้ในขบวนการผลิต , ป้อนเข้าระบบหม้อไอนํ้าและป้อนเข้าระบบหล่อย็น
โรงงานใช้นํ้าจากคลองเป็นแหล่งนํ้าดิบ โดยผ่านกระบวนการตกตะกอนในถังตกตะกอน (CLARIFIER)จากนั้นจึงนํามาผ่านถังกรองทรายกรองความขุ่น ถังกรองคาร์บอนเพื่อกําจัดคลอรีน ถังเรซินเพื่อลดความกระด้าง ถุงกรองผ้าและไส้กรองขนาด 5 ไมครอนและ 1 ไมครอน
โรงงานมีระบบอาร์โอ 2 ชุด
ชุดที่ 1 ออกแบบเพื่อผลิตนํ้า 20 คิวบิกเมตรต่อชั่วโมง , 1 สเตจ ประกอบด้วยเมมเบรน 18 ท่อน ซึ่งติดตั้งอยู่ใน 4 เวส
เซลๆ ละ 6 ท่อน
ชุดที่ 2 ติดตั้งห่างจากชุดแรกหลายปีเพื่อผลิตนํ้า 30 คิวบิกเมตรต่อชั่วโมง , 2 สเตจจัดเรียงแบบ 4:2 เวสเซล คือสเตจ 1
4 เวสเซลๆละ 5 ท่อน , สเตจที่ 2 มี2 เวสเซลๆละ 5 ท่อน
ความเป็นมา/ปัญหา
1) ค่าสารละลายของนํ้าจากแหล่งนํ้าดิบสูงมาก เนื่องจากมีปัญหานํ้าทะเลหนุนในช่วงหน้าแล้ง
2) ค่าสารละลายของนํ้าที่ผ่านระบบอาร์โอชุดที่ 1สูงเกินมาตรฐานของโรงงาน
3) ค่าสารละลายของนํ้าที่ผ่านระบบอาร์โอชุดที่ 2สูงเกินมาตรฐานของโรงงาน
4) ลูกค้าเคยทําการเปลี่ยนเมมเบรนบางส่วนในอาร์โอชุดที่ 1 ประมาณ 7 เดือนก่อน ทีมงานเข้าสํารวจ ทําให้ค่าสารละลายในนํ้าดีขึ้นเป็นปกติแต่หลังจากเปลี่ยนไปไม่นาน ค่าสารละลายก็เพิ่มสูงขึ้นเรื่อยๆจนสูงตามค่าที่กล่าวมาข้างต้น
5) โรงงานต้องทําการล้างระบบ (CIP) สัปดาห์ละ 1-2 ครั้ง เนื่องจากแรงดันนํ้าป้อนและค่าความแตกต่างของแรงดันระหว่างนํ้าเข้าและออกจากระบบ (DELTA P) สูงขึ้นมาก และสูงมากกว่า 7 บาร์ณ วันที่เข้าสํารวจ
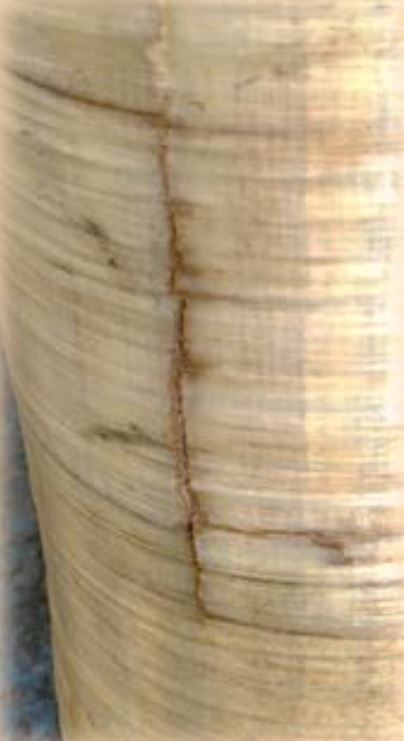
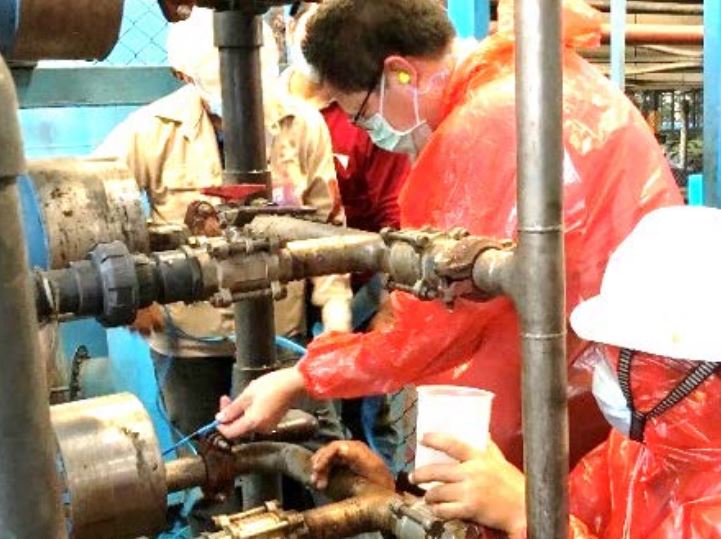
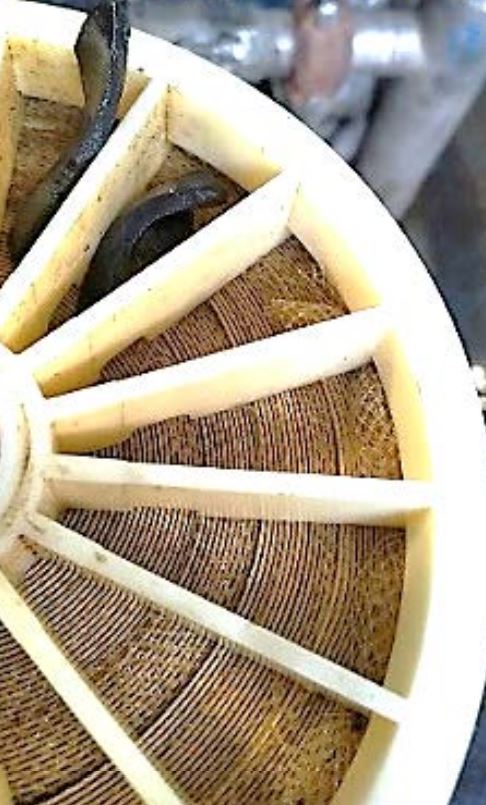
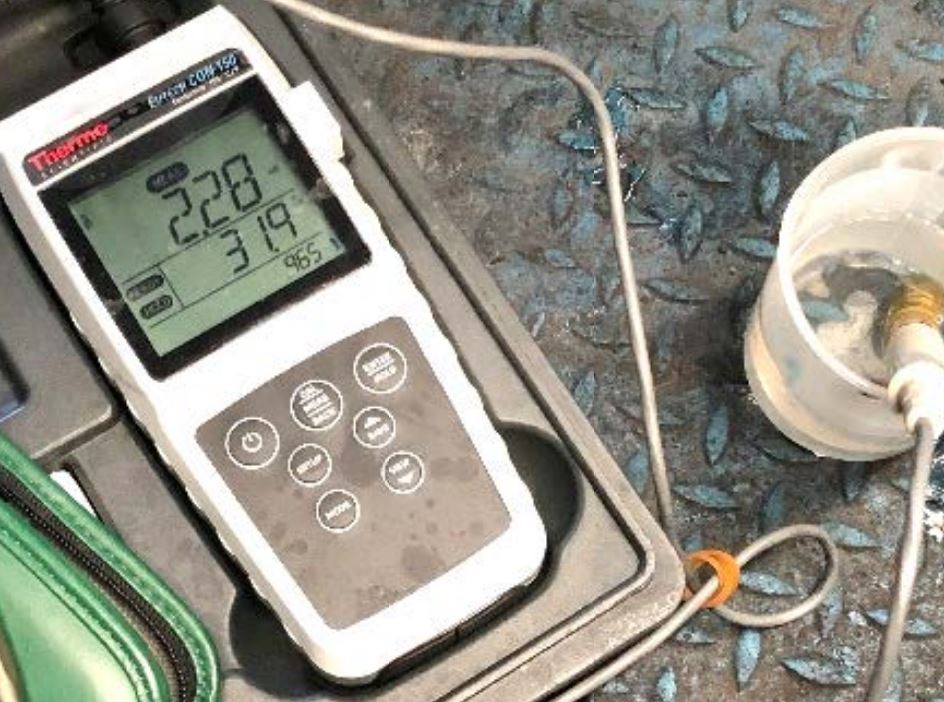
สํารวจระบบและแก้ไข
1) พบว่ามีการเดินระบบโดยปรับลดอัตราการไหลของนํ้าทิ้ง (RO CONCENTRATE )จนเกือบปิดสนิท เพื่อเพิ่ม %
อัตราการผลิตนํ้า (%RECOVERY) ตามคําแนะนําของผู้ขายสารเคมีป้องกันตะกรัน ทั้งที่ระบบอาร์โอชุดที่ 1 และ 2
2) พบว่าการออกแบบอัตราการผลิตนํ้าของระบบอาร์โอชุดที่ 2 ไม่เหมาะสมกับจํานวนเมมเบรนที่ติดตั้งอยู่ ทั้งนี้
อ้างอิงจากการคํานวนด้วยซอฟแวร์ของผู้ผลิตเมมเบรน ซึ่งผลการคํานวนพบว่าจํานวนเมมเบรนและลักษณะ
การจัดเรียงของระบบที่ออกแบบไว้ควรเดินด้วยอัตราการผลิตนํ้าอาร์โอ 25 คิวบิกเมตรต่อชั่วโมง
3) ค่าสารละลายของนํ้าจากแหล่งนํ้าดิบสูงมาก วัดเป็นค่าความนําไฟฟ้าได้5560 ไมโครซีเมนต่อเซนติเมตร
4) ค่าสารละลายของนํ้าที่ผ่านระบบอาร์โอชุดที่ 1 สูงมาก วัดเป็นค่าความนําไฟฟ้าได้2720 ไมโครซีเมนต่อ
เซนติเมตรซึ่งค่า %การกําจัดสารละลายของระบบคิดป็น 52% (มาตรฐาน 95%)
5) ค่าสารละลายของนํ้าที่ผ่านระบบอาร์โอชุดที่ 2 สูงมาก วัดเป็นค่าความนําไฟฟ้าได้3940 ไมโครซีเมนต่อ
เซนติเมตรซึ่งค่า %การกําจัดสารละลายของระบบคิดป็น 29% (มาตรฐาน 95%)
6) จากค่า %การกําจัดสารละลายของระบบตํ่ามาก ทางทีมงานจึงตรวจสอบ
หน้างานด้วยวิธีโพรบบิง (PROBING) ที่อาร์โอชุดที่1 เพื่อค้นหาเมมเบร
นท่อนที่อาจมีความเสียหาย รูพรุนเมมเบรนอาจฉีกขาด หรือมีการดสีย
หายที่โอริงต่างๆและเพื่อเลือกเมมเบรนท่อนที่ยังมีประสิทธิภาพที่ดีเพื่อ
ใช้งานต่อไปได้และถอดเมมเบรนออกเพื่อตรวจเช็คโอริงต่างๆ
ผลการทําโพรบบิงทําให้ทราบว่า เมมเบรนบางส่วนใน RO1 มี
ประสิทธิภาพตํ่ามาก จึงได้ทําการคัดแยกเมมเบรนโดยพิจารณาจากผล
การทําโพรบบิงนี้ได้เป็น 2 กลุ่มคือ
6.1 เมมเบรนที่ยังมีประสิทธิภาพพอใช้นํามาจัดเรียงกลับเข้าในเวสเซลได้18 ท่อน จาก
ทั้งหมด 24 ท่อน ทําการล้าง (CIP) แล้วลดกําลังการผลิตนํ้าลงจาก 20 คิวบิกเมตรต่อชั่วโมง
เหลือ 15 คิวบิกเมตรต่อชั่วโมง
6.2 เมมเบรนที่มีประสิธิภาพตํ่า นําไปทดสอบที่เวิร์คชอป เพื่อล้างภายนอกแล้วนํากลับมาใช้
เป็นอะไหล่ต่อไป
7) จากการทําโพรบบิงระบบอาร์โอชุดที่ 2 พบว่ามีเมมเบรนที่มีประสิทธิภาพดีอยู่เพียง
1 ท่อน จึงแนะนําให้เปลี่ยนเมมเบรนใหม่ทดแทน
ผลการแก้ไข
อาร์โอ 1 : หลังจากคัดเลือกเมมเบรนและติดตั้ง พร้อมทั้งทําการล้าง (CIP)และเดินระบบที่อัตรารผลิตนํ้า 15 คิวบิกเมตร
ต่อชั่วโมง ปรับค่าอัตรานํ้าทิ้ง 6 คิวบิกเมตรต่อชั่วโมงและอัตราการหมุนเวียนนํ้ากลับที่ 4.5 คิวบิกเมตรต่อชั่วโมงแล้ว ทํา
ให้ได้ค่าสารละลายในนํ้าลดลงเหลือ 1200 ไมโครซีเมนต่อเซนติเมตรซึ่งสามารถใช้เป็นการสํารองชั่วคราวได้
จากการติดตามผลหลังจากผ่านไป 1 เดือน ระบบยังเดินต่อเนื่อง โดยยังไม่มีการ CIP ด้วยอัตราการผลิตนํ้าคงที่
อาร์โอ 2 : หลังจากการเปลี่ยนเมมเบรนทดแทน ได้ทําการเดินระบบด้วยอัตราการผลิตตามการคํานวนจากซอฟแวร์ผู้ผลิต
เมมเบรน เปลี่ยนสารเคมีป้องกันตะกรัน สารเคมีป้องกันการอุดตันจากแบคทีเรีย ด้วยอัตราการใช้ที่เหมาะสม ระบบ
สามารถผลิตนํ้าได้อย่างต่อเนื่อง มีค่า %การกําจัดสารละลาย (SALT REJECTION) มากกว่า 95%
จากการติดตามผลหลังจากผ่านไป 1 เดือน อัตราการผลิตนํ้าและค่าแรงดันต่างๆยังคงที่ โดยยังไม่มีการทํา CIP